
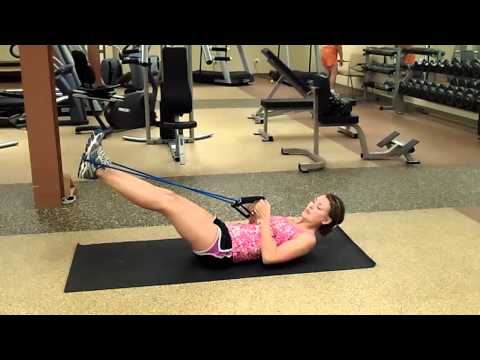
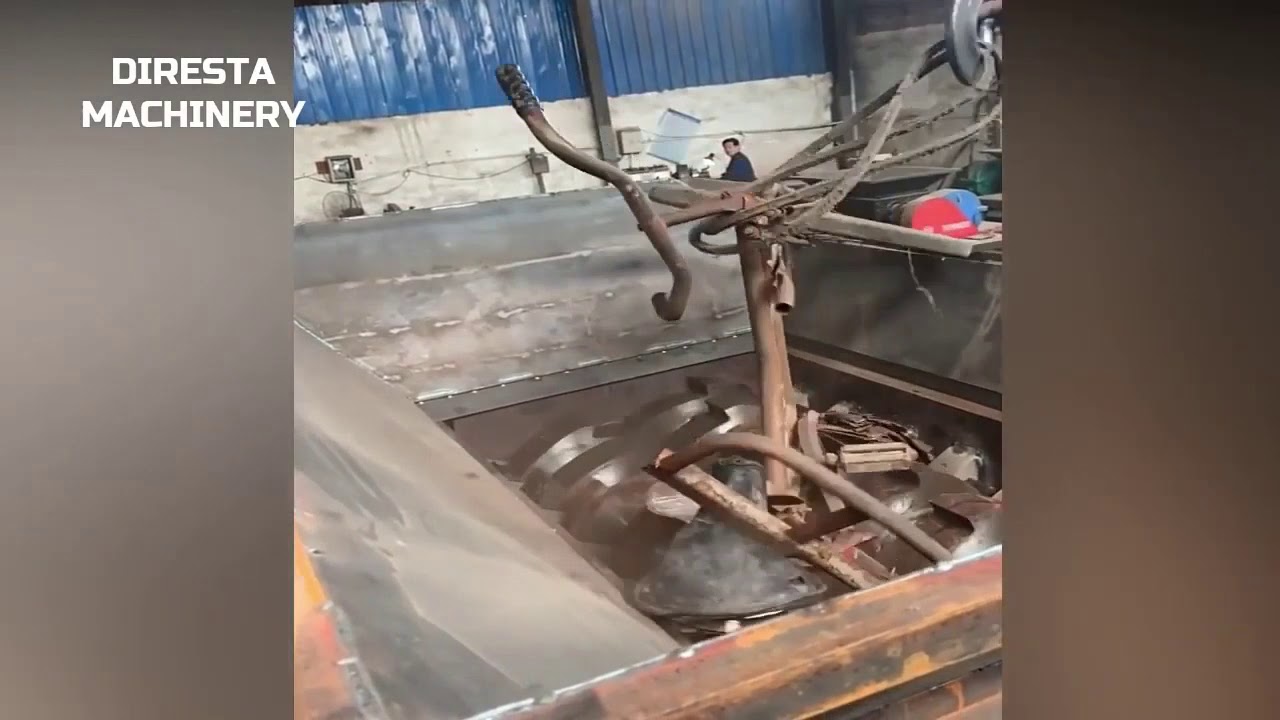
Pneumatic actuators do not use hazardous materials, so they pose no environmental or health hazards. Pneumatic actuators can withstand temperatures from −40☏ to 250☏ (−14☌ to 120☌). Pneumatic actuators routinely have positional errors of 0.1 in. For higher forces, steel actuators have a maximum pressure rating of 250 psi with bore sizes from ½ to 14 in. They are available in bore sizes from ½ to 8 in. Most aluminum pneumatic actuators carry a maximum pressure rating of 150 psi. The piston returns to its original position using a spring or pressurized air supplied to the other side of the piston. This linear motion can move a load or create a force.
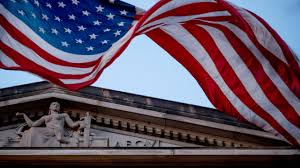
Pneumatic actuators have a piston inside a hollow cylinder that is moved through that cylinder by pressurized air entering from a compressor or pump. Here’s a quick look at each of these methods. They convert energy into a motion or force and are usually powered by one of three methods: hydraulics, pneumatics or electricity. It seems almost all industries use linear actuators in some way-perhaps to move inventory, products, or components, or to carry out manufacturing and assembly processes. Matching a Pneumatic Cylinder’s Output to the Application What’s the Difference Between Roller and Ball Screws? It was originally published April 16, 2015.Ĭomparing Electric and Fluid-Power Actuators
